ENERBIE
conceptualise | develop | construct
Engineering services
ENERBIE-ING
Engineering services are offered under the ENERBIE-ING operating branch, with our main fields of activity being turbo mechanical engineering, sealing technology and plant engineering. We do not shy away from complex and stubborn problems and are also “at home” where it is “hot”, high pressure prevails, components rotate quickly or everything together.
Development ENERBIE-TEC
Enerbie GmbH develops, produces and sells steam and ORC turbines with output powers ranging from a few kilowatts to approx. 10 MW under the operating branch ENERBIE-TEC. In addition, we also offer retrofits and upgrades for existing turbines and support you in the design or analysis and optimization of the entire ORC cycle process and its component
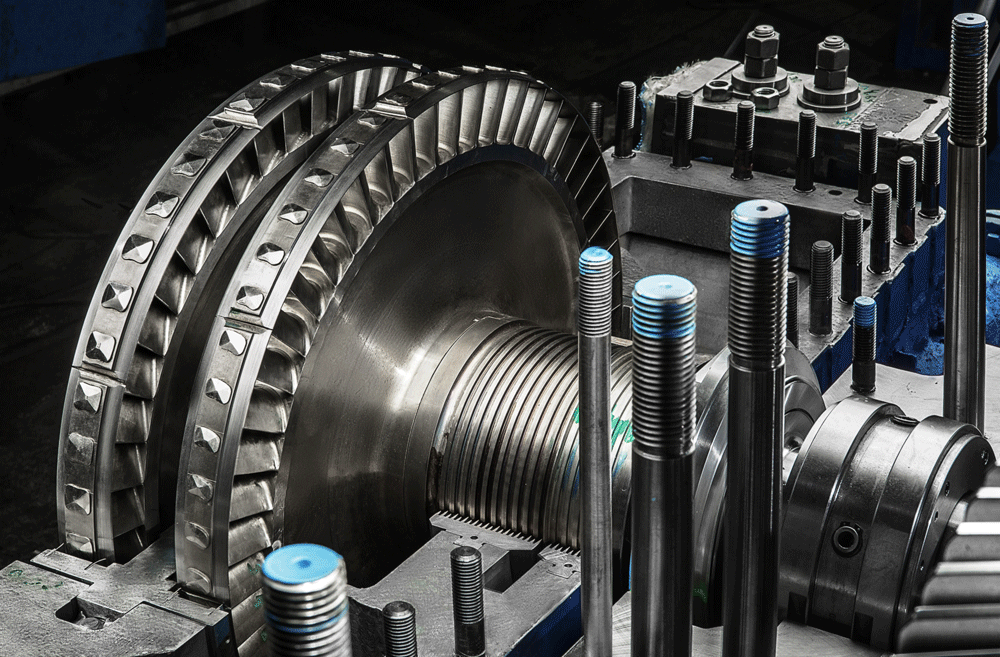
General
Our basic philosophy is simple: In the end, what comes out should be worth more than the work and resources that went into it. We do not apply this consideration to ourselves as a company in isolation, but naturally include our customers and their added value and expenses. In other words, an order is only a good order if everyone benefits from it. Sustainability in a general sense and sustainability of business relationships are our main focus.
Methodology
We are firmly convinced that in mechanical engineering in particular, but also in all other areas of working life, all problems and tasks must always be thought about and approached holistically. Withdrawing to – usually more or less arbitrarily created – balance sheet limits not only almost always brings disadvantages, it also often prevents finding a viable solution at all.
In addition to the holistic view, we are also of the opinion that, in the sense of “from rough to fine”, especially for new products and complex problem solutions, the “First Principal Thinking” concept should always be followed. The systematic decomposition of complex contexts to their original properties and dependencies is one of Enerbie’s core know-how for finding solutions to problems and evaluating different possibilities for new products.
We think from atoms up, through the manufacturing drawings, to the documentation.
Calculations
As mechanical engineers, we are of the opinion that you need numbers for every technical problem that you want to solve or decide. Our tool of choice is Excel. If an appropriate tool is not already available, we create a project-specific one. The bandwidth ranges from a few lines to multi-sheet, complex nested design tools with several thousand lines of code.
The more complex the calculation is, the more important it seems to us that the applying engineer not only has a good basic understanding of the situation, but also knows what specifically happens in the calculation tools and (almost more important) what is not taken into account.
All of the calculation tools we have developed therefore have, from a certain level of complexity, quite deliberately set manual work steps. It has been shown that complete automation, in which one arrives at finished results with only a few simple inputs, often leads over time to the fact that the actually necessary (usually in-house) specialized knowledge is almost completely lost.
Another aspect of results-oriented work that we place a great deal of emphasis on at Enerbie is simple plausibility checks, which are carried out in parallel with the highly complex calculation activities. Since we are aware that virtually all engineering activities are based on assumptions and are thus never exactly correct, we consider it extremely important that the applying engineer, in addition to specialized knowledge, also has a certain feeling for the material and, for example, the resulting forces and stresses, in order to be able to rule out errors at an early stage.
Under the same condition, we used FEM and CFD simulations almost exclusively in conjunction with accompanying analytical calculations in order to have at least a rough orientation regarding the expected results.
CAD and ERP systems
Whenever possible, we work according to the top-down principle. This means that we first design the finished assembly, including all dependencies and rules, in a coherent model and only then derive the components required for it down to the raw parts. The assemblies created in this way are then stored and maintained as templates.
All rules and dependencies, including the explanations, are defined at the assembly level and are not scattered among the individual components. As a result, the time-consuming, error-prone and continuously occurring revision activity for all individual parts that have ever been used is eliminated. Moreover, there is no risk of repeating old errors by using individual parts that have not been used for a long time.
The methods described above can be applied excellently, especially for the single-part and small-batch production that often occurs in industry, as a modification design based on already built assemblies. In addition to the significant time savings, a further advantage lies in the clearly described rules and the resulting much lower susceptibility to errors during design.
In addition, the possibility arises to easily and safely make minor changes to standard designs on a project-specific basis and thus generate added value for its customers without incurring additional costs or expenses. Since the respective template remains unaffected by the project-specific changes, one can focus solely on the current project during construction.